
#Dew point measure portable#
SF82 | Dew Point Control | Compressed Air Dryers () - 100 barg/1450 psig Caption: Portable Fast-Response Hygrometer - Michell MDM50 Measure trace moisture in pressures from 100 barg/1450 psig up to 138 barg/2002 psig We have a wide choice of dew-point transmitters and portable hygrometers that are capable of measuring dew point and trace moisture in gases at various pressures.
#Dew point measure full#


#Dew point measure install#
The sensors are small and easy to install and maintain – especially with the

The measurement performance remains valid and directly related to its factory calibration. This means that as the partial pressure of water vapour increases with total pressure, For any given partial pressure of water vapour there is only one corresponding dew point. Metal oxide moisture sensors directly measure the partial pressure of water vapor. Why ceramic metal oxide moisture sensors are recommended for measuring dew point in high pressure air or gas Reducing the pressure of a gas has a cooling effect, and this,Ĭoupled with the already low temperatures below sea, could easily lead to ice forming in air lines and disable the submarine. The high pressure allows the tanks to be cleared quickly and gives the crew a greaterĪvoiding excess moisture is vital in marine applications because of the risk of freezing.
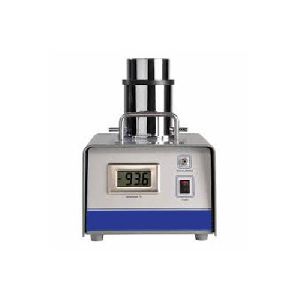
It is often used for clearing submarine ballast tanks for ascent to the surface. High pressure air is used in marine and military applications for breathing and instrument air, as described above. These may operate at 350 bar (5076 psig) through to 700 bar (10,153 psig) so as to supply the fuel quickly.ĭry gas is important to avoid the risk of damaging the engine as well as to avoid the risk of icing up in cold weather. Read more about the critical measurements in breathing air. To keep the tanks small, the air may be pressurised up to 380 bar (5500 psig) and control of moisture is important to avoid bacterial growth or damage to valves. Tanks of breathing air are used for diving, firefighting and working with hazardous materials. Typical applications for ultra-high-pressure air include: In industrial applications, pressures from 20 to 450 barg (290 to 6527 psig) are referred to as ‘ultra-high pressures’. What are the main applications where you would need to measure dew point at pressures over 100 barg? ‘How to calculate pressure dew points (PDP) accurately’ explains the physics that causes this. This makes drying the air especiallyĬrucial and monitoring the dew point of the dry gas not only helps control drying cost but also provides quality checks on the high-pressure air or gas. The main reason to measure the dew point of gas under pressure is to avoid the risk of condensation forming in the system, which can lead to bacterial growth or corrosion of valves.Ĭondensation becomes a risk when gas is pressurized because the dew point of air or gas rises with pressure. Why is it important to monitor the dew point of air or other gases under pressure?
